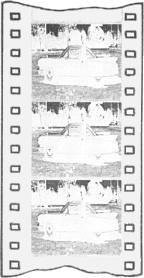 | 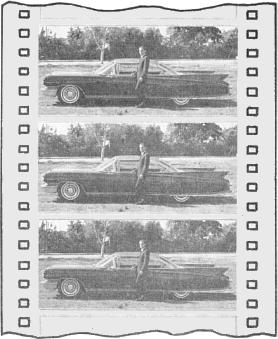 |
IN THE 35MM-TO-70MM print-up process, a standard Panavision 35mm camera negative
(left) produces a high-quality 70mm release print (right) by means of highly sophisticated
optical printing methods developed by Panavision. In the process, the squeezed negative
image is de-anamorphosed and enlarged from 4 sprocket holes in height to 5 and printed
on 70mm positive stock. |
BREAKTHROUGH IN
35MM-TO-70MM
PRINT-UP PROCESS
B y C H A R L E S L O R I N G
WHEN OTTO PREMINGER'S exciting film "The Cardinal" flashed across
huge panoramic screens in premiere roadshow engagements through
out the world recently. It became an important milestone of progress in
motion picture technology. Many veteran film technicians viewing the
picture at Hollywood's Egyptian Theatre on one of the largest existing
screens, assumed they were watching a feature that had been filmed on
65mm color negative for release in 70mm print form, since it had the
sharpness, brilliance and color saturation which they had come to associate
with that process.
In reality, however, what they were seeing was the first feature film
to be printed up from 35mm Panavision to 70mm for wide-screen release.
Since then, "Becket" has been roadshow-premiered using the same process.
"The Carpetbaggers" and several other important features similarly printed
will soon follow.
The new 35mm-to-70mm print-up process is the result of several years
research and development by three companies working closely together:
Panavision, Inc., Eastman Kodak and Technicolor. Thus it was that Director
of Photography Leon Shamroy, ASC, photographed "The Cardinal"
on the new Eastman 35mm Color negative stock, using a new series of
highly improved Panavision anamorphic lenses, and the negative image
was enlarged to produce 70mm non-anamorphic release prints by Technicolor.
In order to appreciate the significance this development holds for the film
industry, it is first necessary to note that the number of theaters equipped
with 70mm projection facilities has been growing far more rapidly than is
generally known. There are now more than 1,100 such installations through
out the world, with more being added every day.
In Japan, for example, there are 71 theaters with 70mm projectors. Korea
has five such houses and Formosa two, with Thailand and Okinawa each having one. There are twelve in Paris. In
many small towns and outlying areas the world over, portable 70mm projectors are being used. The United Kingdom has many 70mm installations,
including seven in London and one or two each in 28 other cities. Austria has
five, Belgium ten, Denmark twelve, Israel five, Argentina four, Chile two
and Sao Paolo, Brazil three.
In many foreign countries there are rigid ceilings on admission prices for
35mm presentations, but a considerable increase is allowed for 70mm showings.
In Mexico, for example, the official government-controlled admission for a
35mm screening is four pesos (32 cents, American), but an increase to eight
pesos is permitted when the film is in 70mm. This means that American producers can look forward to greatly in
creased revenue from foreign releases now that an inexpensive, and technically excellent, method is available for
obtaining high-quality 70mm prints of pictures shot in Panavision 35. The
availability of such prints should, in turn, spur an even greater increase in
the number of 70mm installations worldwide.
According to Robert E. Gottschalk, president of Panavision, Inc., the
70mm format has great boxoffice value because the public has come to
associate it with bigger, sharper and better looking motion pictures.
"This is especially true in Europe and Japan where photography is a
universal hobby and people are more appreciative of photographic beauty,"
he points out. "Since the war, the tremendous growth in 35mm still and
8mm movie making has made something of a photography 'expert' of the
man in the street, to the extent where he is willing to go out of his way to
see a good-looking film-and pay more to see it."
He cites "Lawrence of Arabia,"
filmed in Super Panavision (65mm non-anamorphic negative printed to
70mm) as a prime example of a film whose awe-inspiring photography not
only garnered every award in sight, but helped the film score a sensational
success at the box office-with the average viewer commenting most favorably on the beautiful photography.
In the print-up process, a standard Panavision 35 negative is run through
a highly sophisticated optical printing system developed by Panavision to reproduce faithfully every last bit of
definition available on the original. The optical printer de-anamorphoses
("unsqueezes") the image on the negative frame and enlarges it from four
holes in height to five, printing on 70mm release positive stock.
Many viewers, thinking in terms of the fuzzy blow-ups usually obtained in
enlarging from 16mm to 35mm, are amazed at the sharpness of the result
in print-up from 35mm to 70mm. However, the physical equations involved
are vastly different. The Panavision 35mm negative encompasses, with the
exception of the sound track strip, the total area of the frame (as opposed to
the much smaller "Academy aperture" frame). This means that in anamorphic
35mm photography the negative area used is 63% greater than for normal
1.85 aspect ratio photography, but when enlarged 2 1/4 times in the unsqueezing and enlargement phases during print-up - the final result is projected onto a screen only 25% larger than that which the 35mm print is
meant to fill. This, of course, results in a much sharper screen image in proportion to the area of the positive
frame - and infinitely greater resolution than is possible in blow-ups from
16mm to 35mm.
A comparison of technical data indicates why any picture shot in Panavision 35 can be successfully printed
up, even though such print-up was not considered during filming. The full
aspect ratio of Panavision 35 is 2.35, whereas the full aspect ratio of the
70mm print-up is 2.2. The height which is always the critical dimension
-is the same, but there is a difference in width of 1.5 over all. Divided by
two, with half on one side and half on the other. there is a cut-off on each
side of .075 - a loss so infinitesimal that it cannot be noticed by the average
viewer. This means that the director, during shooting, need not worry about
losing part of his composition in the conversion.
The producer need not decide in advance whether or not he will want a
print-up to 70mm at a later date. He simply shoots in Panavision 35, then,
after the picture is completed and he has looked at his 35mm answer print,
he may find that he has turned out something rather special and that it
warrants roadshowing in 70mm-in which case, he calls the laboratory and
orders the 70mm prints he needs. This is exactly what happened in the case
of M-G-M's new musical, "The Unsinkable Molly Brown," which was filmed
in Panavision 35 with no thought of a 70mm release, but which turned out so
well that print-ups have been ordered for its premiere engagements.
The new process is expected to be a boon to drive-in theater operators, who
have always been plagued by the fact that they must wait until quite late in
the evening to begin their showings in order that the picture might show up
on the screen. Because 70mm projectors use long focal length lenses with
extremely wide apertures, a great deal more light reaches the screen (17 foot
lamberts as contrasted to the 2 footlamberts produced by 35mm projectors in the average drive-in theater).
This enables the drive-in theater owner to present a picture that is as clear
and brilliant as any shown in a "hardtop" theater and to start his shows
much earlier in the evening without worrying about whether his audience
will be able to see the picture. In economic terms, it simply means that he
will be able to present two shows each night instead of only one.
There are a few minor drawbacks to the new process. For one thing, the
70mm prints are considerably more expensive than 35mm prints but this
is offset by the fact that the 70mm prints, because of the wider film, new
projectors and more careful handling in the large format--last infinitely
longer than 35mm prints. It is not unusual for one print to be used in daily
showings at the same theater for an entire year, after which it is carefully
cleaned and sent on for continuing runs in other situations.
Also, while the new Eastman color negative stock is almost grainless,
there is a difference in grain between a print-up and a 70mm print made
from a 65mm negative - a difference that would only be apparent to the
average viewer if the two were projected side by side on a large screen
for comparison.
Because the print-up is an optical, rather than a contact printing process,
there is some slight build-up in contrast with a corresponding slight loss
in tonal range-but here, again, the difference is one that normally is obvious only to film industry technicians.
Gottschalk points out that the print-up process is not meant to replace Super Panavision or Ultra Panavision
(slight anamorphic squeeze processes), both of which involve photography on
65mm negative and are considered productive of the absolute ultimate in
image sharpness and quality.
"These processes, naturally, have far
greater quality on the screen than any print-up process could ever have," he
comments. "They produce a `velvet' appearance, an almost three-dimensional
effect which, when the projection is especially good, makes the screen seem
almost to disappear completely. The Super and Ultra Panavision processes
will continue to be used on multi-million-dollar spectacles like `Lawrence,'
`West Side Story,' and `My Fair Lady,' where the producer wants to go absolutely First Cabin. The print-up process,
on the other hand, has been designed for producers in the medium
budget field for whom, before this development, the advantages of 70mm
roadshow exhibition for their product was completely out of the question."
In the print-up process, the cost of the answer print is greatly reduced because the timings arrived at for the
35mm prints can usually be used without change. Similarly, the sound as
originally recorded can be spread over the 4 to 6 tracks of 70mm prints with
no difficulty.
In making the 70mm print-ups, Technicolor utilizes the latest techniques of liquid-gate or "wet" printing
in which the negative is bathed in liquid as it moves through the printing gate. This not only washes the
negative absolutely clean, but the liquid tends to "fill in" any small scratches or abrasions in the emulsion, resulting in extremely clean, sharp
70mm prints. Without the benefits of liquid gate printing the print-up process would not be practical because dust
and dirt, which seldom can be completely eliminated in such an operation, would be enlarged along with the
picture.
Panavision's new print-up process should open vast new horizons for the
medium-budget film producer desiring the increased quality, and revenue,
that a 70mm release can produce.
|